Working in a warehouse can be demanding. Especially in a material handling environment. Warehouse safety for the warehouse workers should be at the top of your list to help ease the physical demand but also provide a safe working environment.
Common warehouse hazards can be overlooked, but easily remedied. should include incorporating procedures and systems that protect employees from injury while maintaining productivity. Safety equipment, safety procedures, and periodic safety training should already be in place. Identifying potential safety hazards should be reviewed periodically; tripping hazards, possible falling objects, hazardous chemical storage, possible manual lifting, and proper lifting techniques, and the list goes on.
Reviewing your existing warehouse safety rules and a safety checklist is a good start. Below are some other warehouse safety tips that can help contribute to better warehouse safety management.
Eliminate manual box opening
Opening boxes in any receiving department can be a tedious, repetitive affair that can quickly become dangerous due to worker fatigue or lack of attention. Any time employees are using sharp objects as part of their job duties may increase the likelihood of injury.
To eliminate these risks entirely, consider purchasing an automatic box opening device that will remove human interaction entirely from the cutting process. This device will reduce the potential for employees’ injuries and will increase productivity across the department.
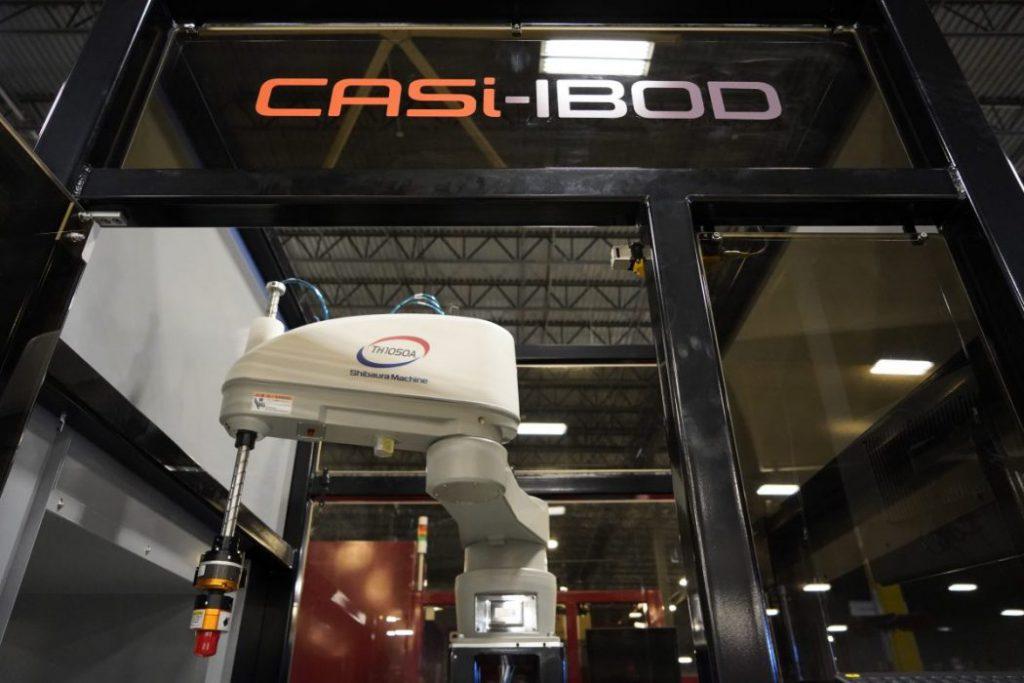
Shorten the moving distance
Carrying heavy items across a warehouse is often a necessity that can’t be eliminated by automation. However, often equipment and technology can minimize the need for employees to carry products or shipments from point A to point B.

Consider adding transport carts, conveyor belts, or roller tables to your operation to reduce the amount of manual operation required to move items throughout your warehouse. Ensure conveyors are staged at an ergonomic height for operators to reduce back strain issues and make objects easier to handle.
These solutions, when strategically placed, can significantly reduce injuries associated with tripping or falling, as well as preventing damage to the items that are a possibility inherent in manual handling operations.
Prohibit overloading carts
While warehouse procedures are a constant across every industry, one often overlooked requirement is mandating the weight and height of items that may be transported by cart. By not including this requirement, the cart can tip over onto an employee, resulting in harm or a loss of product.
To eliminate overloading carts, make sure your warehouse has a clear policy on how much weight is acceptable for any mode of transport. Be sure to label different carts with their appropriate weight limit, and train employees on how to properly follow the procedures. While limiting the amount of weight on carts can slightly reduce productivity, it will ultimately ensure that your employees are protected from avoidable accidents.
Organize your warehouse with the employee in mind
Often a warehouse is organized based on what product comes in first, or what items are sold more often. While it is important to consider your workflow when organizing items on your shelves, it is more vital that you consider the impact the placement will have on the employees who have to deal with those products on a daily basis.
Organize your shelves to place large, heavy, or bulky items between the knees and shoulders of an average sized employee. The heaviest items should be placed between the knuckles and elbows. This makes it easier for employees to retrieve items from the shelves without straining their backs or being hit by falling packages.
Keep your warehouse spotless
A messy or cluttered warehouse is a recipe for disaster. The additional hazards created by a disorganized warehouse put your employees at great risk for injury.