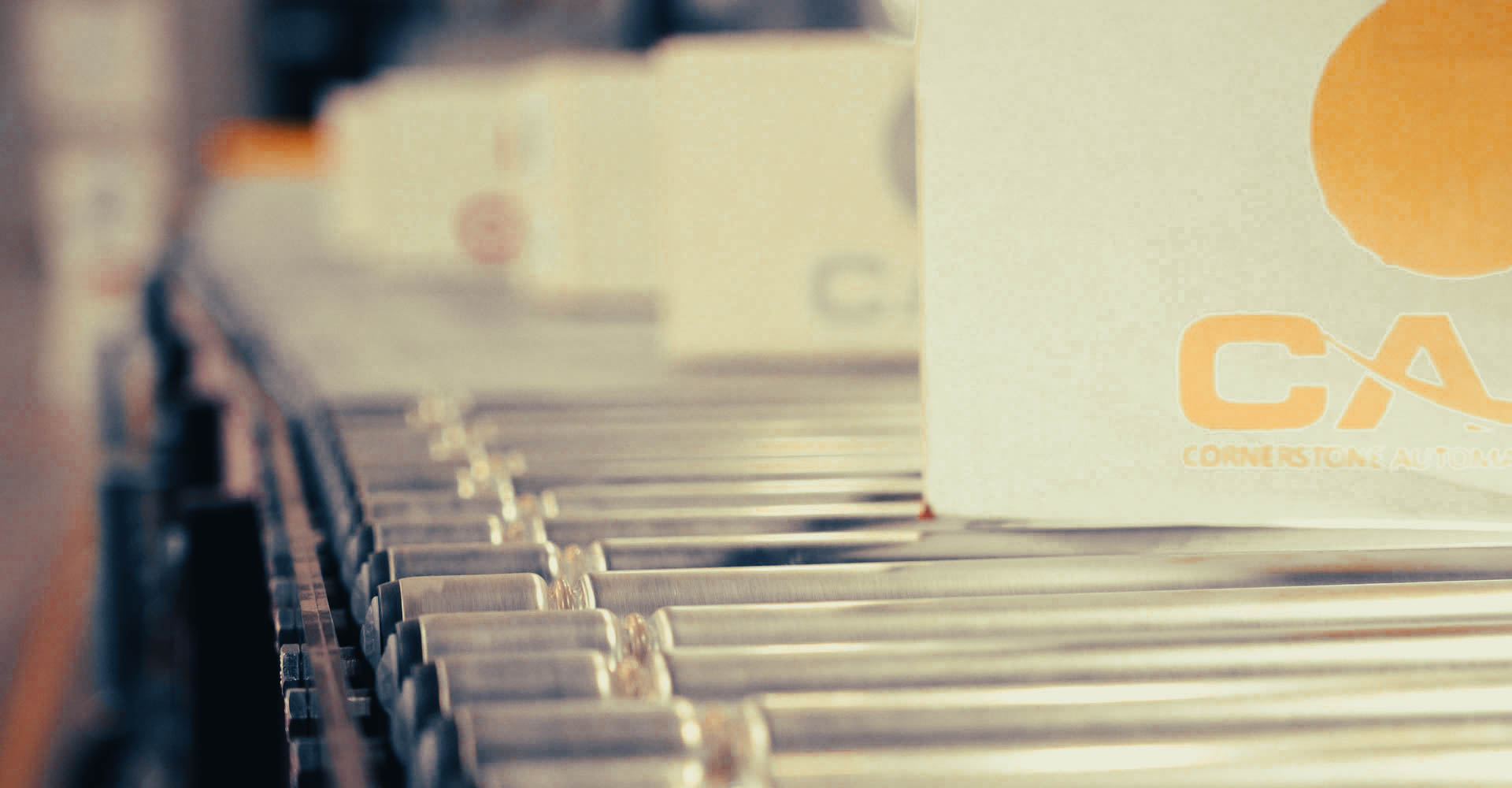
CASE STUDIES
When we are presented with problems, we find solutions. Here are our stories.

ELIMINATING HUMAN ERROR AT HUDSON NEWS
“At Hudson News, our return processing center ships unsold inventory from our retail stores back to the publisher. We receive shipments from our depots all across the U.S., repackage them and then send them back to the publisher for a refund.
“We had 8 employees handling returns before we bought the CASI system. Because of the large amount of returns we deal with, there was always the potential for human error. For example, employees would send products back to the wrong publisher. When the publisher would ship those incorrect returns back to us, we were responsible for paying the return freight costs. So, in addition to the time spent dealing with errors, there was also a financial aspect to it as well.
“With the CASI machine, we have reduced the number of employees working returns down from 8 to 2. The machine is so accurate that we don’t have to worry about human error anymore. I can’t tell you exactly how much money and time we have saved in the 4 years we’ve been using the CASI machines, but it is not insignificant.”
RELIABLE SUPPORT
“There were some issues that I didn’t know how to fix when I first started working with the CASI machine. If it stopped working because of a misaligned sensor, I had no idea where to look to have it back up and running. But CASI was always there to train me on all of the solutions for hardware issues. Whenever I reach out to them for help they respond within 30 minutes. The customer service is very responsive, which makes my job a lot easier.
“I would absolutely recommend CASI. The accuracy of their machines is far better than manual sorting, and it will eliminate human error almost entirely from your operation. With the savings in labor and time, purchasing a CASI is an easy decision.”
-Ricardo Bach
Book Return Supervisor